Microfabrication of a Diffractive Microlens Array on n-GaAs by an Efficient Electrochemical Method
ZHANG L, MA X Z, ZHUANG J L, et al.
Microfabrication of a Diffractive Microlens Array on n-GaAs by an Efficient Electrochemical Method [J]. Advanced Materials, 2007, 19(22): 3912-8.
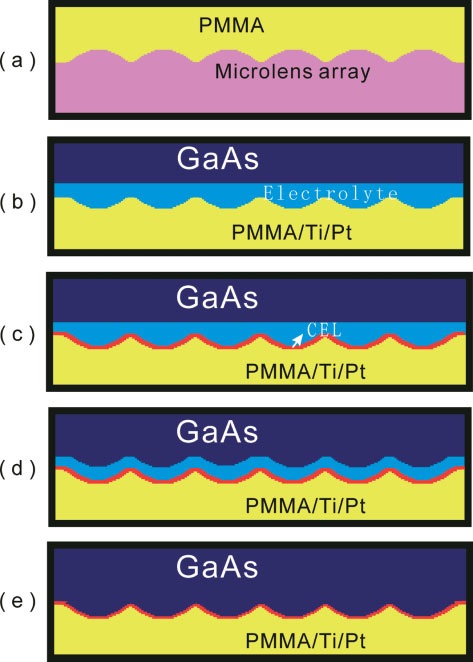
Scheme 1. Schematic illustration of the confined etchant layer technique(CELT) process in the micromachining of an 8-level microlens array.a) Imprinting a negative copy of the microlens array from the quartz on to the PMMA. b) The PMMA evaporates with Ti and Pt and is used as a working electrode or mold in the CELT. c) A thin etchant layer is generated on the mold (working electrode) by adding a scavenger to the solution. d) GaAs starts to be etched by approaching it to the mold once the CEL touches it. e) A complete negative copy of the mold with 3D microstructures is fabricated on GaAs, which is also approximately the same as the microlens array on quartz.
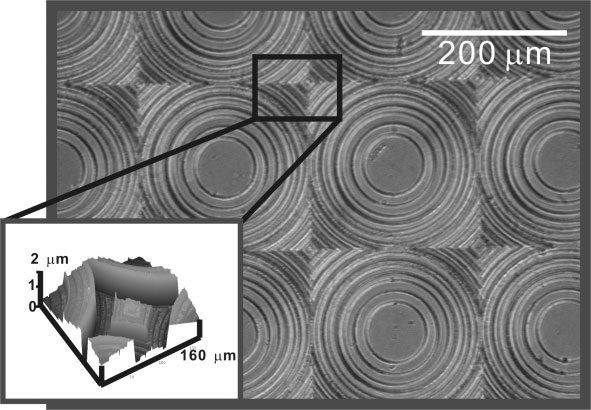
Figure 1. The AFM (insert) and microscope images of microstructures on the PMMA mold surface.
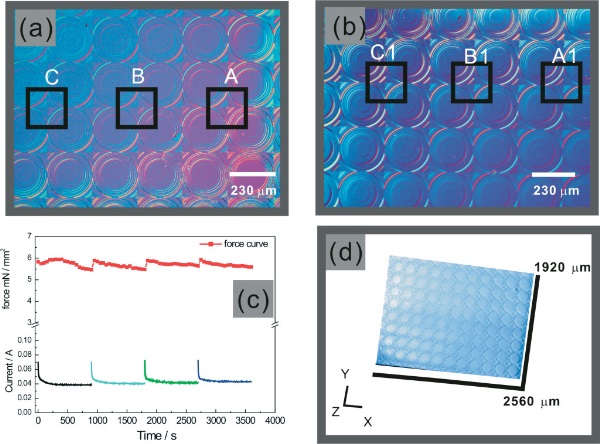
Figure 2. Microscope image of the microlens array fabricated in a solution of 3.32 × 10–2 mol L–1 HBr + 9.96 × 10–2 mol L–1 L-cystine + 0.5 mol/L H2SO4; the force between the mold and the substrate is around 6 ± 0.2 mN mm–2. a) Without refreshing the solution. b) With refreshing the solution.c) The curve showing the change of the force and the corresponding i–t curve in the process of micromachining with CELT. d) Microscope image of the fabricated microlens array on a large scale.
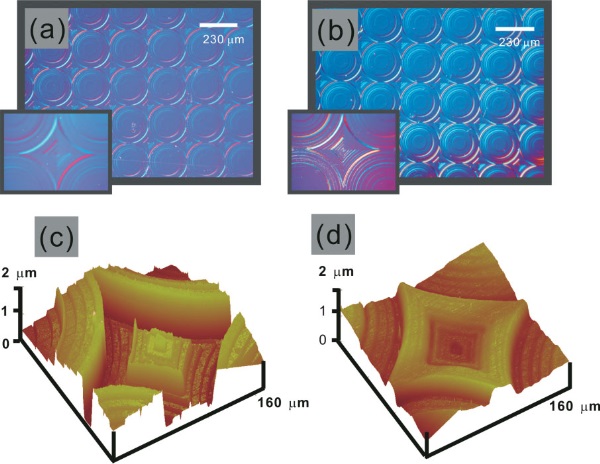
Figure 3. The microlens arrays fabricated with different concentrations of Br–: a) 3.32 × 10–2 mol L–1>HBr + 9.96 × 10–2 mol L–1 L-cystine + 0.5 mol L–1 H2SO4. b) 9.96 × 10–2 mol L–1 HBr + 9.96 ×10–2 mol L–1 L-cystine + 0.5 mol L–1 H2SO4. c) AFM image of the conductive mold. (d) AFM image of the fabricated microstructure in the same solution as in Figure 3b.
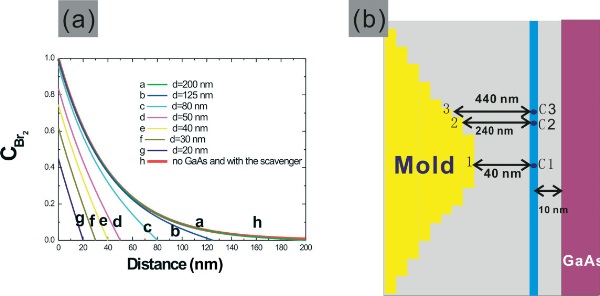
Figure 4. a) The concentration profile of Br2 when the GaAs is kept at different distances from the mold surface. b) Schematic model to illustrate the concentration difference affected by the distance between the mold and the workpiece.
文章链接:http://onlinelibrary.wiley.com/doi/10.1002/adma.200700300/abstract